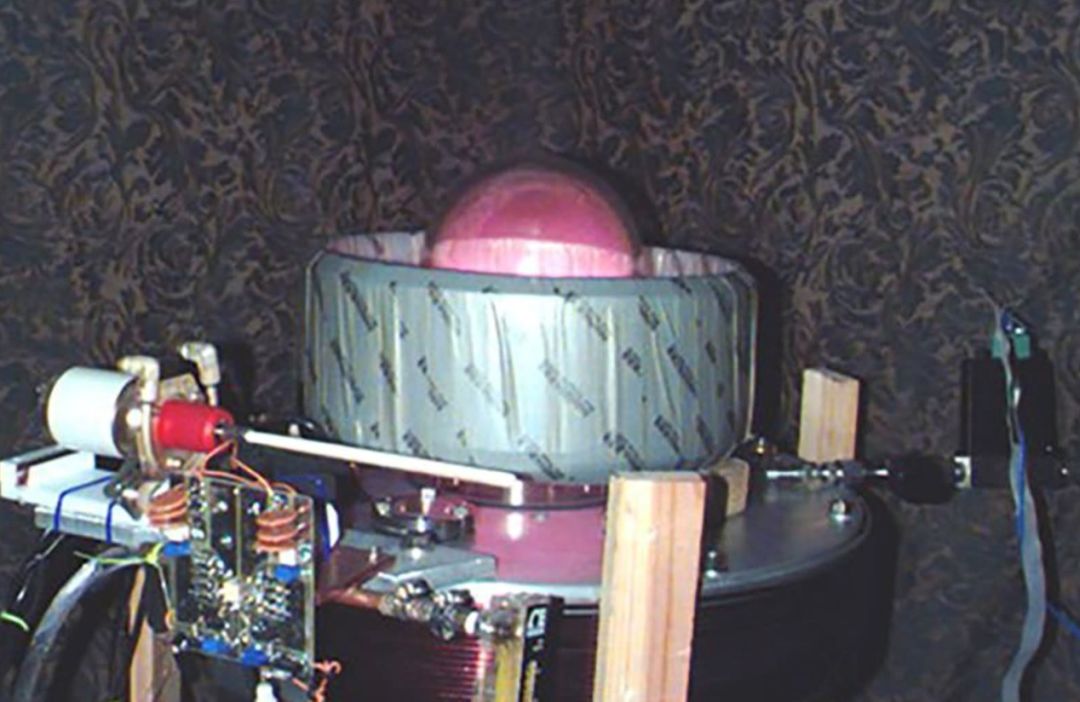
文章摘要
半导体制造的核心挑战之一在于如何在极小的硅片上精确蚀刻出复杂的电路图案,以满足现代电子设备对更高性能和更小尺寸的需求。随着技术的进步,传统的蚀刻工艺逐渐难以满足日益增长的精度要求。为了应对这一挑战,加州大学洛杉矶分校的研究团队经过20年的努力,开发了一项名为DirectDrive的突破性技术,该技术通过快速切换射频能量,显著提高了等离子蚀刻的精度和效率。
DirectDrive技术的核心在于其能够在50微秒内快速切换射频能量,从而实现对等离子体的精确控制。这种快速切换能力使得蚀刻工艺能够在更短的时间内完成,同时减少了误差和缺陷。与传统的蚀刻方法相比,DirectDrive技术能够以埃级精度蚀刻出更小、更密集的半导体器件,这对于下一代电子产品的开发至关重要,尤其是在人工智能和高速计算领域。
这项技术的研发过程充满了挑战和突破。早在2006年,Patrick Pribyl就提出了通过控制射频能量来改善蚀刻工艺的想法,并在自家厨房中搭建了初步的实验装置。然而,将这一想法转化为工业级技术需要多年的研究和实验。Pribyl与物理学家Walter Gekelman合作,共同筹集资金并建立了实验室,通过激光和定制探测器详细研究了等离子体的行为。他们的研究不仅揭示了等离子体的复杂运动,还为将这一技术规模化提供了科学依据。
DirectDrive技术的成功不仅在于其技术上的突破,还在于其对半导体产业的深远影响。该技术能够支持环栅晶体管、6F2 DRAM和3D NAND器件的微缩,并可扩展至4F2 DRAM和互补场效应晶体管等先进器件。这些器件需要极其精确的蚀刻步骤和极紫外光刻图案,才能形成复杂的3D结构。DirectDrive技术的应用,使得这些器件的制造成为可能,从而推动了半导体技术的进一步发展。
尽管DirectDrive技术在实验室中取得了显著成果,但其从实验室到工厂车间的转化仍需时间。研究人员通过计算机建模和实验测量,逐步将这一技术推向工业化生产。目前,基于DirectDrive技术的等离子刻蚀设备已经在芯片制造厂中投入使用,能够快速生产出先进的电路。这一技术的成功,不仅展示了科学研究的长期积累和突破,也为未来半导体技术的发展奠定了坚实的基础。
总的来说,DirectDrive技术的出现标志着半导体制造领域的一次重大进步。通过提高蚀刻精度和效率,这项技术为下一代电子产品的开发提供了强有力的支持,同时也展示了科学研究在推动产业进步中的重要作用。
原文和模型
【原文链接】 阅读原文 [ 2205字 | 9分钟 ]
【原文作者】 半导体行业观察
【摘要模型】 deepseek-v3
【摘要评分】 ★★★★★